粉末冶金金属基固体自润滑材料摩擦学行为
2012-06-07作者:李溪滨 刘如铁 程时和 李美英
(中南工业大学粉末冶金研究所、粉末冶金国家重点实验室)
摘 要:本文在分析粉末冶金金属固体自润滑材料减摩机理的基础上,研究了孔隙度和固体润滑剂对材料摩擦学性能的影响。研究表明:在材料结构组成、原始粉末粒度组成及其分布,固体润滑剂纯度及其结构等基本一定的情况下,随着孔隙度的增加,材料的摩擦系数和磨损速率提高;固体润滑剂的增加,在一定范围内,其减摩性能得到改善,导致材料摩擦系数和磨损速率降低,从而显示出粉末冶金金属基固体自润滑材料摩擦学的某些规律性行为。(中南工业大学粉末冶金研究所、粉末冶金国家重点实验室)
关键词:粉末冶金;孔隙度;固体润滑;摩擦学
粉末冶金技术制造现代固体自润滑复合减摩材料具有许多独特的优点,特别是在耐磨性方面大大优于铸造材料。多年的实践经验表明:采用粉末冶金技术生产的铁基和铜基烧结轴承材料,其使用寿命一般是青铜、黄铜、巴氏合金、铸铁、钢制滑动轴承以及滚动轴承等的1.5~3倍[1]。然而,粉末冶金材料由於存在孔隙,并且添加了不同种类和数量的固体润滑剂,导致其在物理机械性能的某些方面不及铸造材料。因此,本文结合作者和前期研究工作的资料,着重探讨了孔隙度和固体润滑剂对材料摩擦、磨损和润滑性能的影响,以期揭示该类材料的某些内在规律性,制备出物理机械性能和摩擦磨损特性优化组合的金属基固体自润滑材料。
1 孔隙度对材料摩擦磨损的影响
在经典的固体磨损理论中,涉及到孔隙度和固体润滑剂的理论计算公式不多见,这是因为它们研究的对象大多数是致密材料。以阿查德(Archard J.F.)建立的粘着磨损理论和概括微观切削机理建立的目前较为公认的磨粒磨损理论为例,其推算出理论计算公式,即单位滑动距离的总磨损率为:
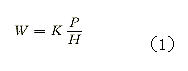
然而在该计算公式中,并未涉及到孔隙度的影响因素。应该指出,孔隙度(应还考虑到孔的数量、孔径大小、孔的形状及其分布等因素),对材料的物理机械性能可产生本质的影响,进而对材料的摩擦磨损特性必将建立内在的联系。从(1)式中可以知道,磨损率是与较软材料的硬度成反比,而在弹塑性材质范围内,其硬度与强度有着密切的相关性。因此,早期研究工作者在这方面作了许多工作,并且得到多个适应范围不同的关系式。F.P.克努德森(Knudsen)报导了材料强度与原始粉末粒度直径D和孔隙度ε(%)有如下的实验关系式[2]:
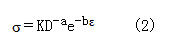
从(2)式可以得到:当粉末粒径一定时,材料强度随着孔隙度的增加而下降;当孔隙度一定时,强度随着粒径的增大而降低。
为了建立粉末冶金多孔材料与其致密材料之关系,许多研究工作者作了大量的理论计算和实验研究工作,并且得到适应不同孔隙度范围的相关计算公式。E.赖斯凯维茨(Ryshkawitsh)报导在孔隙度为(0~30%)范围内的经验公式[3]:

从(3)式中,可以得出同样一个结论:即孔隙度的增加,材料的强度值降低。
本文作者研究了铜合金基的固体自润滑材料孔隙度与摩擦磨损性能之间的关系,该材料由基材Cu-Sn-Zn-Pb,微量强化元素Ni,Mo,以及固体润滑剂石墨和二硫化钼等组合而成。图1表示出材料孔隙度与摩擦系数和磨损率之间的关系。实验条件为载荷:76N,速度:2.0m/s,对偶材料:GCr15合金铜,环境:干摩擦。从图中的实验曲线可见,随着孔隙的增加,材料的摩擦系数和磨损速率是提高的。

图1 铜合金基固体自润滑材料中孔隙度对摩擦磨损性能的影响
中南工业大学方宁家、徐润泽等研究了Fe-3Cr-2Ni-2Cu-0.8C-3WC材料的相对密度对磨损性能的影响,图2表示实验相关曲线[4],实验条件:载荷:2MPa,滑动速度:0.79m/s,对偶材料:3Cr2W8V(HRC∶35~40)。从实验曲线可知,在室温或500℃的磨损试验中,随着材料密度的增加,亦即孔隙度的减少,磨损率是下降的,不过在室温中曲线下降的斜率更大一些。

图2 Fe-2Cr-Ni-2Cu-0.8C-3WC材料的相对密度对磨损的影响
图3列出了铜粉烧结材料孔隙度与硬度的相关实验数据[5],从中可见,随着孔隙度的增加,材料的硬度值降低。
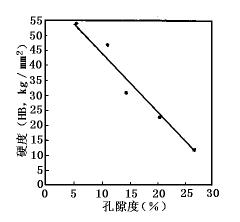
图3 铜粉烧结材料孔隙度与硬度的关系
从经验和计算公式(2)、(3)以及上述实验研究工作结果表明:孔隙是产生磨屑的基源,它以边缘碎裂和撕裂的两种形式产生磨屑,其磨损机理是以磨粒磨损为主;同时,孔隙亦是材料微裂纹产生和破坏的应力集中区,是导致材料机械性能降低的主要因素(如强度、硬度等)。随着孔隙度的减少,孔隙的作用将由强变弱,材料的强度和硬度提高,磨损机理可能转变为混合磨损机理为主;材料密度愈高,粘着磨损的程度增加。在不考虑材料本身含油的状态下,在设计和制造粉末金金属基固体自润滑材料时,希望孔隙度较小为宜。显然,在不同的使用工况下(如载荷、速度、温度、润滑方法等),孔隙度的影响和作用也不完全一样。
2 固体润滑剂对摩擦磨损性能的影响
粉末冶金固体自润滑材料的固体润滑剂是以一种结构组元加入到复合材料之中。固体润滑剂的加入主要产生两种影响,一是可以改善两个相对运动摩擦表面的摩擦、磨损和润滑性能,一是影响材料的物理和机械性能。粉末冶金固体自润滑材料的润滑薄膜的成膜机理与常规采用的表面成膜方法不完全相同,以现今Z普遍使用石墨和二硫化钼为例,常规使用主要有三种方法:即把固体润滑剂渗入适当的树脂和粘结剂中,并胶涂在摩擦表面;或把固体润滑剂细粉喷涂和渗入到摩擦表面中;或通过摩擦表面的化学反应来形成固体润滑膜。然而,粉末冶金固体自润滑材料本身含有固体润滑剂,在磨合过程中,利用自身的固体润滑剂在摩擦表面间形成一层薄的连续润滑膜,并且靠本身“自耗”来不断补充和提供固体润滑剂,使其修复被撕裂或破伤的润滑膜,从而达到自润滑和减摩作用。
不少摩擦学研究工作者对薄膜润滑理论进行了大量的理论研究和科学实验工作,并且得到了一些被公认的结论。诺贝尔奖获得者、美国物理学家布立基曼(Bridgeman)考虑到薄膜的塑性变形对接触区的影响,提出由压力下薄膜的剪切强度Sp来代替滑动表面上薄膜的低剪切强度Sf[5]:
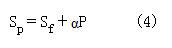
当固体润滑膜展开在摩擦表面时,则复合材料的摩擦系数与表面间薄膜形成的程度有关,其混合规则为:

将(4)式两边同除P,则可以得到固体润滑膜的摩擦系数fs:
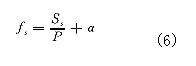
从(5)、(6)式中可知,复合材料的摩擦系数与基体材料的摩擦系数,材料硬度和固体润滑剂的剪切强度有关。
粉末冶金固体自润滑材料的磨损主要由粘着磨损,磨料磨损和疲劳磨损等机理产生。其中粘着磨损的体积磨损量与施压的正压力P、滑动距离S成正比,与磨损基体的硬度成反比,这是粘着磨损的宏观规律。一般磨损方程为:
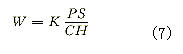
本文作者研究Cu-Sn-Zn-Pb-Ni-W-C复合材料中,石墨含量对材料摩擦系数和磨损性能的影响,实验结果如图4所示。从实验曲线可以看出,随着石墨含量的增加,材料的摩擦系数和磨损率降低。图5是本文作者研究不同材料中二硫化钼含量与摩擦系数和磨损率的关系。曲线1为二硫化钼含量与银基材料的磨损率关系;曲线2和曲线3是二硫化钼含量与高温镍合金基材料磨损率和摩擦系数之间关系。实验结果同样表明:随着固体润滑剂含量的增加,材料的摩擦系数和磨损率都呈下降规律,从而可以说明,该类材料在既定的试验条件下,二硫化钼已在摩擦表面间形成了一层连续的润滑膜,改善了摩擦表面间摩擦学特性。由於fs《fm,当摩擦表面固体润滑剂的覆盖愈大,fs的主导地位愈显著,那么复合材料的f值就会变小,这与本文作者研究工作的结果是一致的。
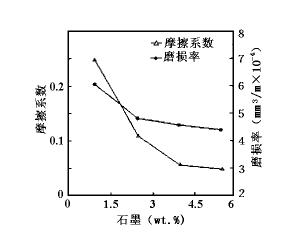
图4 铜合金基材料中石墨含量对摩擦磨损性能的影响
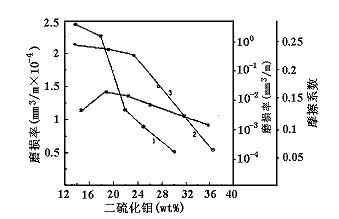
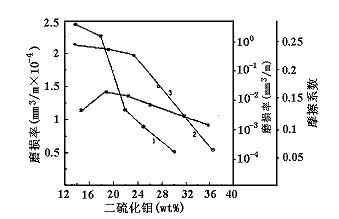
图5 不同基材中,二硫化钼含量对摩擦磨损性能的影响
应该指出:由於现代减磨材料的使用工况存在巨大的差异,例如滑动速度由几个mm/s到100m/s以上,载荷由0.1MPa到10~20MPa以上,温度从负几十度到1000℃以上等,因此,不可能制造出一种能在各种工况下都能使用的减摩材料。然而,粉末冶金固体自润滑材料由于在制备工艺和结构组成等方面都有很大的优越性,所以,该类材料在高温(>400℃)、低温、惰性介质、腐蚀性介质、真空、辐射、污染、一次性润滑以及频繁逆转的装置中等工况下,得到了特别青睐。同时,本文研究的孔隙度和固体润滑剂等影响因素,也必须根据材料的使用工况和对材料的综合性能要求来确定孔隙度的大小和固体润滑剂的种类和含量,才能得到满意的摩擦学特性。3 结论
本文就粉末冶金固体自润滑材料的孔隙度和固体润滑剂对其摩擦磨损性能的影响进行了研究和分析,可以得到如下相关结论:
(1)粉末冶金固体自润滑材料孔隙度的存在,与材料的机械强度和硬度有着密切的内在联系,并且已建立了相应的理论和经验计算方法,从而直接影响到材料的摩擦磨损性能。研究工作表明,随着孔隙度的提高,材料的摩擦系数和磨损率都相应增加。
(2)粉末冶金固体自润滑材料的结构组元固体润滑剂的存在,有利于摩擦表面间摩擦学特性的改善,其以“自耗”机理来提供和补充润滑源,以期形成连续的固体润滑膜。在一定范围内,随着固体润滑剂含量的增加,复合材料的摩擦系数和磨损率降低。
(3)粉末冶金固体润滑材料在干摩擦状态下,其孔隙度必须得到有效的控制;而固体润滑剂的含量,在既定使用工况下,必须兼顾材料的物理机械性能和摩擦学特性的综合作用,只有这样才能取得满意的效果。
参考文献
[1]и.м.费多尔钦斜著,李孔兴译,粉末冶金复合减摩材料,北京粉末冶金研究所,北京,1985,P18。
[2]F.P.Knudson,J.Amer.,Coram,Soc.,42,376,1959.
[3]H.H.ЩерБань,Порщковая МеталлfрГИЯ,No.9,1973.
[4]徐润泽编著,粉末冶金结构材料学,中南工业大学出版社,湖南长沙,1998,P231。
[5]H.H.Hausner,Handbook of Powder Metallurgy,New York,Chem.Pub1.Co.,1973,P482.
来源:《润滑与密封》