渗碳件表面碳含量分析
2016-11-01谢玲珍
(山推工程机械股份有限公司)
渗碳件表面碳含量及其分布梯度对渗碳层的性能有重要影响。表面碳含量过高、过低或表面脱碳等都将对渗碳件表面强化效果产生不良影响。我公司生产的某种渗碳件工艺方法为渗碳→炉内风冷→机械加工→加热淬火→清洗→回火→磨削,渗碳后重新加热淬火过程中使工件表面发生轻微脱碳,再采用磨削的方法去除脱碳层,同时修正淬火过程中发生的畸变,可以有效提高产品尺寸精度。本文结合我公司生产实际,对渗碳件的表面碳含量分布情况进行检测分析,确定脱碳层深度并验证磨削加工余量的合理性。
1.试验方案
渗碳件材质20CrMnMo,表面碳浓度要求0.75%~0.95%,渗碳有效硬化层深度1.8~2.4mm,表面硬度56~62HRC。由于渗碳件的形状结构不便于表面碳的检测,使用随炉试样进行代表性检测。随炉试样规格φ25mm×50mm,材质20CrMnMo,数量6个。渗碳设备为易普森多用炉生产线TQF-27-ERM。
渗碳件材质20CrMnMo,表面碳浓度要求0.75%~0.95%,渗碳有效硬化层深度1.8~2.4mm,表面硬度56~62HRC。由于渗碳件的形状结构不便于表面碳的检测,使用随炉试样进行代表性检测。随炉试样规格φ25mm×50mm,材质20CrMnMo,数量6个。渗碳设备为易普森多用炉生产线TQF-27-ERM。
(1)渗碳。随炉试棒标识1-6号,随工件渗碳后炉内风冷,渗碳工艺曲线见图1。

(2)二次淬火。渗碳风冷后4~6号试棒随工件重新加热淬火,气氛碳势设置为0.18%,加热至840℃±10℃保温1h,好富顿K油淬火。
(3)试样制备。试棒从端部线切割制取φ25mm×10mm表面碳试样,并标记检测面及标号1~6。
(4)表面碳检测。①清洁表面碳试样。②用千分尺测量试样原始长度并记录。③平面磨削量0.1mm,测量长度并记录。④直读光谱仪检测表面碳含量并记录。⑤每磨削0.1mm测定长度及碳含量一次。
(5)有效硬化层深度检测。对4~6号试棒采用维氏硬度计检测硬化层深度。
(6)渗碳件实物剖检。对渗碳件进行实物剖检硬化层深度及金相分析。
2.试验结果及分析
共对6个试样进行了8次磨削及表面碳含量的检测。各试棒的单次磨削量、累计磨削量及相应的表面碳含量记录见表1、表2。
共对6个试样进行了8次磨削及表面碳含量的检测。各试棒的单次磨削量、累计磨削量及相应的表面碳含量记录见表1、表2。
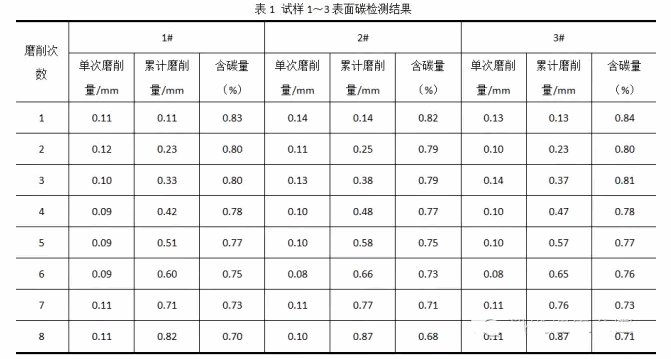
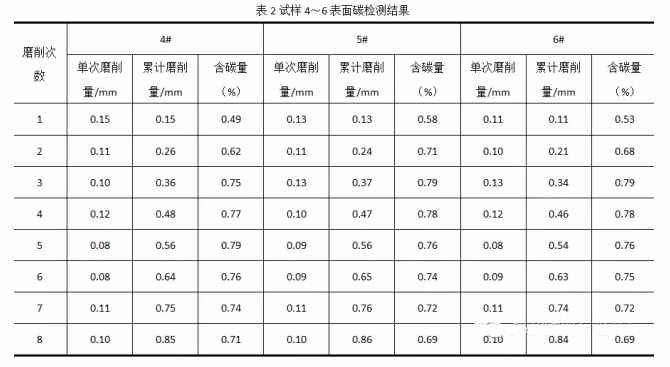
根据表格数据绘制表面碳含量的分布梯度曲线,见图2,1~3号曲线为渗碳——风冷后进行检测得到的曲线,4~6号为渗碳→风冷→二次淬火后得到的曲线。

4~6号试棒淬火后硬化层检测结果为2.3~2.5mm,略高于工艺要求上限。
根据试验数据可知1~3号试棒在渗碳风冷后表面碳含量在0.8%~0.85%之间,表面碳含量分布曲线在近表面层平缓下降,多用炉密封性能及气氛保护效果较好;而4~6号试棒由于在二次加热时气氛碳势设定比渗碳时低很多,因此表面碳含量在表层发生明显“低头”现象,0.1~0.15mm深度处碳含量在0.49%~0.58%。以表面碳含量0.75%为界限则试棒脱碳层深度约在0.29~0.36mm,工艺要求磨削余量在0.3~0.4mm,因此渗碳件磨削后能够保证一定的表面硬度及耐磨性,磨削后的硬化层深度也能满足产品的Z终要求。
渗碳件磨削后的剖检结果如表3所示。

3.结语
根据对渗碳随炉试样及渗碳件的检测结果,表面碳含量的分布控制合理,渗碳淬火后磨削预留量合理,磨削后工件表面无脱碳层,既满足了表面硬度及耐磨性能,也利于尺寸精度的提高。
根据对渗碳随炉试样及渗碳件的检测结果,表面碳含量的分布控制合理,渗碳淬火后磨削预留量合理,磨削后工件表面无脱碳层,既满足了表面硬度及耐磨性能,也利于尺寸精度的提高。
来源:《金属加工:热加工》2016年第15期